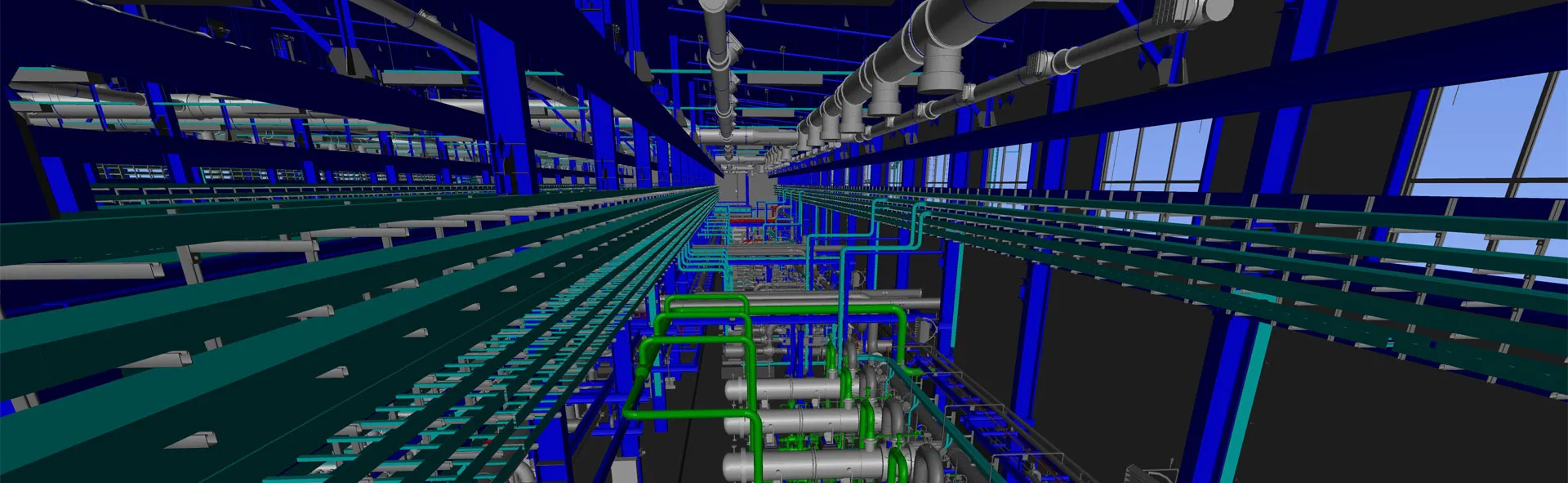
Traditional design is when a 2D model acts as a construction facility and designers work separately, each on his/her own section:
- architectural
- structural
- engineering systems, etc.
Therefore, when the traditional approach is used, problems of then arise such as:
- numerous collisions when bringing the sections together
- lack of access to the up-to-date information
Example. The designer of electrical networks can work with an unfinished construction project, which is why his systems will be incompatible with the finished room during installation. If such conflicts are recognized at the design stage, the participants in the process will have to work long hours to redesign, which is fraught with unpredictable project delivery dates and additional costs.
However, an even more serious problem arises in a situation where collisions reveal themselves on the construction site. Disruption of the construction schedule may result in significant expenses for the developer, which will affect the project prime cost.
BIM (Building Information Modeling) is an information modeling technology that includes elements of a geoinformation system and a computer—aided design system. It makes it possible to design any facilities — buildings, engineering networks, roads. Due to BIM, the building appears as a single whole: its parts are interconnected, and when any changes are introduced, the system automatically recalculates all parameters. This allows avoiding mistakes in design and construction and the need to adjust the drawings many times.
According to the estimates of the Ministry of Construction of the Russian Federation, introduction of BIM technology allowed:
- to reduce errors and inaccuracies in the project design documentation by 40%;
- to decrease the design time by 20-50%;
- to curtail the time for approval and coordination of the designs themselves within the project organization by 90%;
- to cut down the time for checking the project by 6 times;
- to reduce by half the construction investment phase terms;
- to decrease the construction periods and the costs of correcting defects by 4 times.
- Installation solutions
- Construction solutions
- Electrical solutions
- EC&I solutions
- PID development in systems related to 3D design systems
- 3D application at the «Design» stage
- Availability of reporting forms according to certain templates in 3D (specifications, lists of pipelines, data sheets)
- Release of drawings from 3D
- Consideration of the model at 30%-60%-90% stages
- Evaluation of the 3D development of the facility (status system)